The Ultimate Guide For Learners And Buyers
Are you planning to buy a blister packing machine? We know that buying a blister packing machine can be a tough job especially when you do not have expertise in it. Interesting thing is that – you are not alone. After helping 1000+ customers buying the right blister packing machine, we have planned to make the most detailed guide on how to buy a blister packing machine without having technical knowledge.
The guide is easy to read and follow whether you are in your early 20’s or 50+ age. Anyhow, if you still need our help in selecting the right model of blister packing machine, our technical team is available 24/7 for your help free.
Which things do you need to know before buying a blister packing machine?
- A brief knowledge about blister packing machines and their applications
- Your careful attention for 15 minutes to read this guide.
Yes, only 15 minutes you need to understand, how to buy a blister packing machine and you will pass through the whole steps.
In this guide, you will cover.
Chapter 1: Blister packing machine overview
Chapter 2: Working principle of blister packing machine
Chapter 3: Types of blister packing machine based on
Operation Method
Technology (Packing Material Used)
Chapter 4: Main parts of blister packing machine
Chapter 5: Materials used in the blister packaging process
Chapter 6: Quality parameters checking of blister packing machine
Chapter 7: Troubleshooting of common problems, which occurs during operation
Chapter 8: Factors you need to consider while importing a blister packing machine
Chapter 9: Merits and demerits of blister packing machine
CHAPTER 1
Blister Packing Machine
Blister packing machine is equipment, which consists of stationary (non-movable), and moving components. These components aid to seal final products in the pockets or cavities.
By doing several mechanical steps, it forms pockets or cavities on forming material fills the pockets or cavities and covers them with a fitting material.
Hence it assists with setting up the medicine and nutraceutical items for safe conveyance.
Reading further this guide, you will learn the features of this machine, which can enhance productivity in Chapter 4.
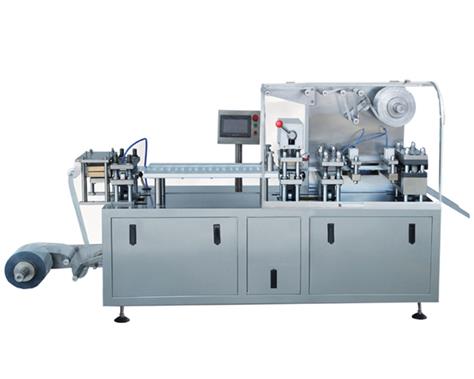
CHAPTER 2
Working principle of Blister packing machine
You have taken the blister packing machine overview in Chapter 1. Now after reading you must be thinking that
- How does this machine work?
- How various parts of this machine work together?
Well, that is what you are going to learn in this chapter.
For your ease, only the general working principle is covered in this guide.
Now let’s start!
The machine works on the rotary sealing principle. This film is moving ahead from a reel and enters in a blister forming unit where the film is softened by heat and forms blisters, then the filling process starts, and after filling the package in blisters, sealing part of the machine sealed the blisters. At the end printing of batch number, start in the printing section and the blistering process complete.
The above summary of the working principle consists of 06 steps. Let us briefly go through all these steps.
Step 1: Turning on the machine
As you turn on the machine, you will notice that feeding rollers and other parts of the machine start moving.
At this stage, the forming film moves to the first stage.
Step 2: Heating Station Processing
Thermoforming blister packing machine includes this heat-processing unit.
At this stage, the machine starts to heat the forming film to the desired temperature until it is soft enough to form cavities. The set temperature is always base on the type of forming material you are using.
Step 3: Film Cavities Forming
In the third step, two mechanisms are used to form desire cavities i.e. compressed air or die plates.
These cavities form the blister packing machine will cool down these cavities to give them a rigid shape.
Step 4: Product filling and Empty cavities checking
In this stage, the blister packing machine will fill the cavities with the final product. The filling step will be either manual or automatic, which totally depends on the type of machine you have selected.
You know that aluminum is opaque (you cannot see through) in nature so it is mandatory to look for empty cavities. Therefore, this empty pocket detector is placed at the end of the filling station.
Step 5: Blister Sealing
At this stage, the filled cavities are ready for sealing. To seal the blister lidding material is used. It is very important for a machine that lidding material is in place timely as forming film reaches the sealing station.
Moving further the lidding material cover the fill cavities. The heat-sealing station comes next which seals the product in the cavities. To make sure that sealing is up to the mark both high temperature and pressure are applied.
Step 6: Printing & trimming of product
This is the last step of blister packing. The seal pack moves to the next stage i.e. printing station. At this point machine, emboss the set message in it.
After that machine, push forward the blister pack to the cutting or trimming station. This trimmer trims it into desire units.
The leftover lidding and forming material is rolled into a scrap collector.
CHAPTER 3:
Types of blister packing machine
Dear readers, it is very important for you to know about various types of blister packing machines.
As you have already study about its overview and its working principle in chapter 1 and 2 now we will discuss its various types.
It is also very important for you to know every machine’s technical specifications which you will read in Chapter 12.
Without wasting any time now let us dig into it.
There are several ways to classify these machines. However, in this guide, you will learn about the types based on their operation and the packing material used. There are the following three types of packing machines based on their operation
- Thermoforming Blister Packing Machine
Thermoforming is a method in which PVC sheets heat by heating plates before inserting them in the blistering machine. By heating, it can be converted into different shapes. Thermoforming is lighter packing.
- Cold forming Blister Packing Machine
There is no use of heat simple sheet is used in a simple shape. Cold forming is somewhat heavier than thermoforming.
- Thermoforming + Cold forming Blister Packing Machine
This type of blister packing machine uses both thermoforming and cold forming mechanisms to pack the product into blister form. It uses the same thermoforming packing phenomena and adds a final layer of aluminum by the cold forming method.
Technology (Packing Material Used)
Based on the technology blister packing machine is comprised of
- PVC/Alu
- Alu/Alu
- Alu/PVC/Alu
- PVC/Al
As, PVC use as forming film and aluminum as the lidding material, this machine is also known as the plastic – aluminum blister pack.
This machine makes cavities in the plastic film material by using thermoforming techniques.
- Alu/Alu
The use of the cold forming technique in this machine makes it different from PVC/Al packing machine.
This machine form cavities by stamping mechanism on aluminum laminate. It uses aluminum foil as a lidding material.
You do not have to preheat the aluminum film in Alu/Alu blister packing machine.
- Alu/PVC/Alu
This equipment also refers to a tropical blister-packing machine due to having an extra aluminum forming and sealing station.
The thermoforms PVC Alu blister-packing machine, seals it again with tropical aluminum.
You can also name it a Thermo-cold forming due to its unique design.
CHAPTER 4:
Main Parts of Blister Packing Machine
Let us recall what you have studied in chapter 1.
“A blister packing machine is an equipment consist of stationary and moving parts”
As you study above that, this machine is a combination of both stationary and moving components. On a serious note, this machine has 100+ parts but we will concentrate only on the main parts.
- Touch Screen Panel
- Feeding Rollers
- Electric Motor Cabinet
- Heating Box
- Cavity Forming Mechanism
- Product Feeding System
- Heat Sealing Mechanism
- Tearing Line Pressing Mechanism
- Tow Mechanism
- Scraper Collector
- Blanking Mechanism
- Touch Screen Panel
The touch screen panel serves as a person-to-machine interaction. Good quality touch screen panels assist in performing and managing tasks easily. It helps the operator in performing:
- Evaluation of production status and statistics.
- Troubleshooting the exact part which indicates on the screen
- Operational configuration: Operator adds operational parameters and machine runs accordingly.
- Feeding Rollers
Feeding rollers play role in the blister packing machine by pushing final products (drugs or food items) to stage one of the packaging processes. These rollers continuously move in a rhythmic pattern along with other machine parts.
The movement of these rollers achieves by electric motors, which you will study in the next subheading.
Effective movement of feeding rollers is achieved by
- The operator handles its movement during operational configuration.
- After which it continuously move in a rhythmic pattern
- Electric Motor Cabinet
Electric motor cabinets aid in the movement of all the moving parts of the machine.
The movement of the mobile parts is transfer through various gears, belts, and shafts.
This cabinet also plays a key role in controlling the moving components’ speed in order to complete the packaging process.
- Heating Box
The heating box is used to heat the packaging material to the right temperature. This temperature ensures that the material is ready for forming in the next step.
This box is consists of a total of 09 parts. These parts can be purchase separately in the future.
- Cavity Forming Mechanism
This is the stage where the blister packing machine is ready to make pockets or cavities. These cavities serve to fill your final product i.e. tablets or other dosage forms.
This part of the machine consist of a total of 18 parts. Again you can replace any of these parts with a new one in the future if declare faultily.
All these 18 parts mutually coordinate with each other to make a suitable cavity shape, which will serve your purpose.
Interesting thing is that you can modify these 18 parts according to your packaging process requirement.
- Product Feeding System
The product feeding system function is to feed the formed cavities with your final product. Your final product could be pills, tablets or capsules, etc.
Normally the product feeding system rate is directly proportional to the rate at which the blister packing machine is making the cavities.
Right after this feeding system empty pocket detector equipment is placed. Most of the machines use photoelectric mechanisms to detect empty pockets.
The purpose of this equipment is to make sure that no cavity will blister if empty.
- Heat Sealing Mechanism
A heat sealing machine is used to seal the filled cavities in the next stage. These cavities are sealed in the form of blister packaging. Just like other components, this equipment is also made up of several parts and different configurations.
- Tearing Line Pressing Mechanism
This pressing machine is used for the permanent sealing of blisters by pressing at high temperatures.
- Tow Mechanism
A tow mechanism is used to move the sealed packaging after pressing the process to the next level for systematic sealing.
- Scraper Collector
The application of Scraper collector is to collect scraper from forming material and sealing machine.
- Blanking Mechanism
The blanking mechanism involves the cutting of the final blister. Our desired number of pockets on the blister decides the size of the blister.
CHAPTER 05:
Material use in blister packaging
You know this chapter will give you a good inside of packaging materials used for packaging.
For your convenience blister packing material is discussed briefly in this chapter.
Blister packaging has vast application across the pharmaceutical industries this packaging provides protection to the medicine and help people to take the proper amount of medication
Blister packaging is made up of several types of polymers, including:
- Polyethylene terephthalate (PET)
- Polyvinyl chloride (PVC)
- Polyvinylidene chloride (PVDC)
- Polychlorotrifluoroethylene (PCTFE)
- Cyclic olefin polymers (COP)
CHAPTER 06:
Quality parameters checking of blister packing machine
So, up till now, you have studied a lot about blister packing machines. Now let us discuss the key quality parameters which you need to consider while importing this machine
- Testing of Logic Controller (Programmable Processer)
- Verification of NMI (Man Machine Interface)
- Recovery System (Power & Emergency Failure)
- Verification of Emergency Operations
- Alarms verification
CHAPTER 07:
Trouble shooting of common problems, which occurs during operation
Every machine can cause an error during its operation. But you can troubleshoot if you have good knowledge of a particular machine. Let us discuss some common problems which may occur during machine operation.
- Opening of safety protection cover.
- Very low pressure of compressed air.
- Low level of Aluminum foil or PVC film.
- The feeder is empty during operation.
- Overload on the machine at any station.
- Overloading on the circuit.
All you need to do is to stop the operations whenever you face the above problems.
Common Issues
Other common issues may occur during
- Formation of Blister
- Heat Sealing
Formation of your required blister is what you are expecting from a blister packing machine. But what to look for if you do not get the right blister at the end?
- Check
- The compressed air pressure
- The heating temperature
- The PVC is qualified or not
- The cooling system is functioning properly or not
- The PVC adheres to the heating device properly
If you are not getting the desire blister packaging then there might be a problem in your heat-sealing area. You may look for
- Cooling systems work normally or not
- Sealing mold is qualified or not
- Abnormal resistance from aluminum foil roll
- The heating device causing too high or too low temperature
CHAPTER 08:
Factors you need to consider while importing a blister packing machine
Honestly speaking there are a lot of factors that you need to consider while importing the blister packing machine. Below are some major factors you look for while importing the right machine.
- Machine Design
- Technical Specifications
- Suitable Brand
- Price
Machine Design
Machine design is a key factor to look for while importing blister packing machines. It will truly depend on what is your final product for packing. For example, if your final product is a tablet then you will select the machine for the solid dosage form.
Technical Specifications
What is your production capacity?
What is your product range for packing?
The above question answers will help you in finding the right machine.
Suitable Brand
Always look for a suitable brand while importing blister packing machines. Being a reliable and key player in the blister packing machine market, you should consider leading brands.
Price
There are several factors that define the price of the blister packing machine. These factors include
- Demand and supply of machine
- Design and construction
- Brand
Keynote is that you should always buy the blister packing machine directly from a manufacturer in order to get the most competitive price for your machine.
CHAPTER 9:
Merits and demerits of blister packing machine
In this chapter, you will learn about blister packing machine merits and demerits.
Merits:
Following are the merits of the blister packing machine.
- Freshness
Medicine retains its freshness due to blister packing and may store for a long duration without having any contamination issue.
- Good protection
Blister packing provides full protection to the medicine, due to its effective sealing ability, it remains medicated substances waterproof, rustproof.
- Dosage size
We can provide effective dosing to consumers due to blister packing.
- Visibility
The consumer can check medicine by seeing without touching it.
- Security
Blister packing provides security to material from damage during transfer.
- Customization
Due to blister packing, we can use the required amount without wasting the rest of it.
- Demerits:
Following are the demerits of this machine.
- We can not use blister packing for all pharmaceutical medications.
- Blister packing can confuse the patient who uses the dosage, which is risky.
- It is a costly and time taking process.
Conclusion:
Blistering machines come in many designs and options. They range from different working principles, design configurations, production capacities, features, etc.
But I believe with this guide, you can certainly choose a perfect machine for your blister packing applications.
Now, it’s your turn to make a move:
Which of the above blister machines fit your packaging needs?
Or, are you facing any challenges with the blistering machines?
Let me know by leaving a comment below.